NASA’s metal additive manufacturing (AM) efforts have entered a new phase of maturity as engineers shift attention toward extremely large, feature-dense components. According to Paul Gradl, Principal Engineer at NASA’s Marshall Space Flight Center, the agency is now 3D printing rocket engine hardware that approaches two meters in diameter and nearly three meters in height, using directed energy deposition (DED). These parts feature complex internal geometries with “thousands of cooling passages” for advanced propulsion systems for commercial space partners and potentially on NASA’s super-heavy-lift Space Launch System (SLS). The SLS rocket will power the agency’s return to the Moon program: Artemis, and enable the establishment of an off-world base for future missions to Mars.
Gradl explained that laser powder bed fusion (LPBF), once at the frontier of AM innovation, has become sufficiently stable for routine use. “We’ve gotten to a semi-normalisation with laser powder bed fusion. It’s something that we don’t even think twice about using now,” he said, noting that while nuance and qualification efforts persist, the real frontier now lies in large-scale DED and new materials.
Join NASA’s Paul Gradl and other AM leaders at Additive Manufacturing Advantage: Aerospace, Space & Defense. Final free registration spots – secure your place for Thursday now.
3D printing timelines have expanded dramatically. Whereas typical metal AM projects see parts printed in days or weeks, these next-generation components may require months of continuous build time, sometimes approaching a full year, when including design and setup. The scale and duration present new challenges in terms of thermal management, error detection, and building interruptions. “We have hard lessons learned regarding build interruptions from powder bed fusion,” Gradl noted referencing a combustion chamber failure, highlighting the need for robust early error detection.
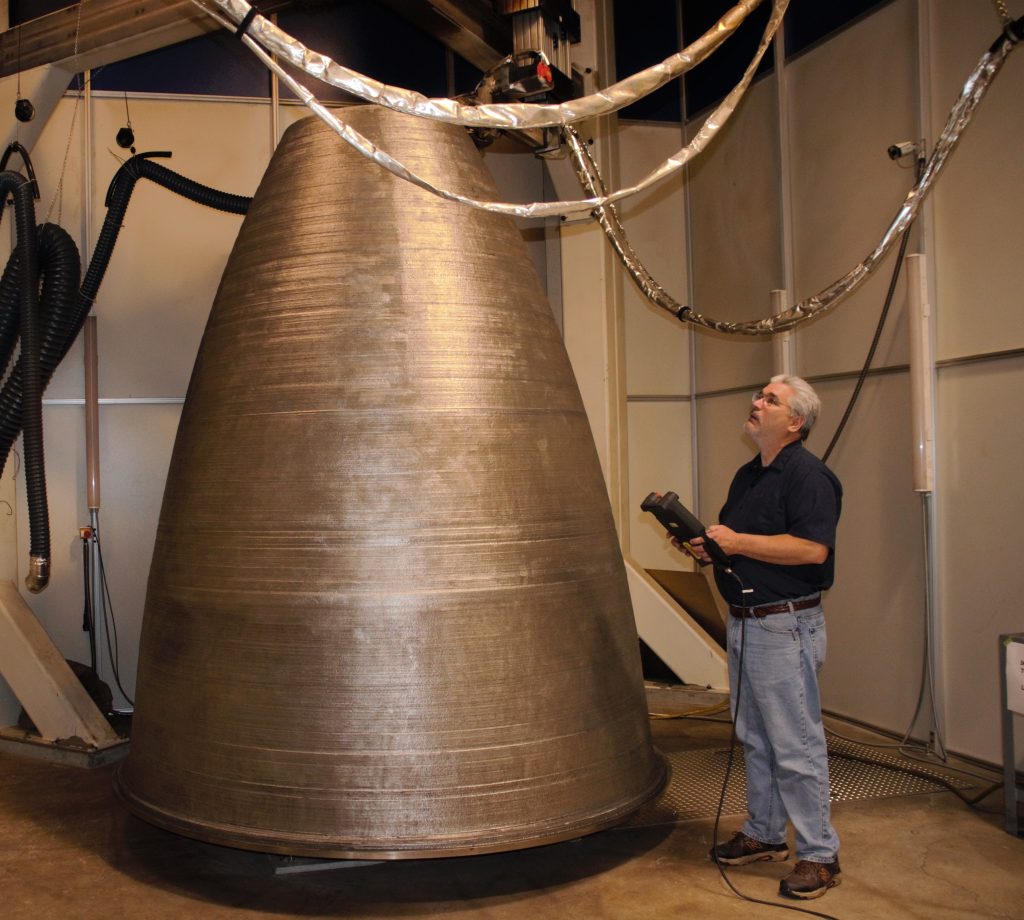
Unlike PBF, which is sensitive to build pauses, DED processes are “almost continuous build interruptions with every layer,” according to Gradl. As parts cool between successive toolpaths, some taking hours per pass, planned interruptions become inherent to the workflow. The use of several tonnes of unmelted powder per build requires staged powder reclamation and restarts, making build interruptions “a lot more tolerable” than in powder bed processes.
Material science has played a pivotal role in this transition. NASA’s GRX-810, a nickel-cobalt-chromium alloy designed for high-temperature, high-strength use, has now entered commercial availability. “We get 1,000 times better creep at temperatures up to about 1100°C,” Gradl said, positioning the material as “fundamentally changing the way we design” in long-life high temperature propulsion systems. GRX-810 incorporates oxide dispersion strengthened (ODS) feedstocks, coating metal powders with compounds like yttria to create materials that withstand ultra-high temperatures.
Speed in alloy qualification has also improved. While GRX-810 took roughly 18+ months from simulation to build, a new oxygen-resistant alloy (internally referred to as ORCAlloy or Oxygen Resistant Compatible alloy) reached build readiness in just three months. Gradl attributes this vigorous pace to advances in computational tools such as Integrated Computational Materials Engineering (ICME), proprietary feedstock production techniques, and increased machine stability.
The acceleration has moved the industry from constrained options, “any colour as long as it’s black,” as Gradl joked, to bespoke alloys tailored for specific propulsion environments. While AM was once synonymous with Ti-6Al-4V and stainless steel, the materials palette now includes purpose-designed formulations inaccessible to processes such as casting or forging.
According to Gradl, the industry is approaching a significant inflection point in materials for extreme environments. “In 10 years, we will probably see a different landscape of materials than we do today,” Gradl said. “We’re making alloys that are required for high temperature, high pressure, extreme environments, and taking advantage of the process for that.”
A core challenge remains cultural rather than technical. Gradl noted that organisations are more comfortable adopting modified versions of known alloys, such as Inconel 718, than accepting new chemistries, even when the performance is equivalent or superior. “There’s still a lot of psychology in how materials are being adopted,” he said. “If it has the same name, companies and agencies are a lot more comfortable with it.”
However, Gradl cautioned against premature claims of qualification. “There’s a different definition of qualification,” he explained. “We want to see a material that is really matured—not just understanding the build parameters but all the subsequent properties and process sensitivities… how it’s going to machine, how it’s going to weld.” NASA intends to publish a framework later this year for materials qualification in aerospace contexts, aiming to standardise what constitutes a mature material.
Gradl also acknowledged broader pressures, including supply chain risk and critical materials. While avoiding specific geopolitical commentary, he noted that NASA is using ICME to explore reductions in the content of costly or scarce refractory metals. “If I had a material like a C-103 that’s 80 or 90 percent niobium, can I reduce that to 40 or 50 percent and add other materials?” he said. The agency is simulating thousands of potential chemistries to identify equivalent performance with more readily available elements, an approach that could reduce reliance on supply-constrained inputs.
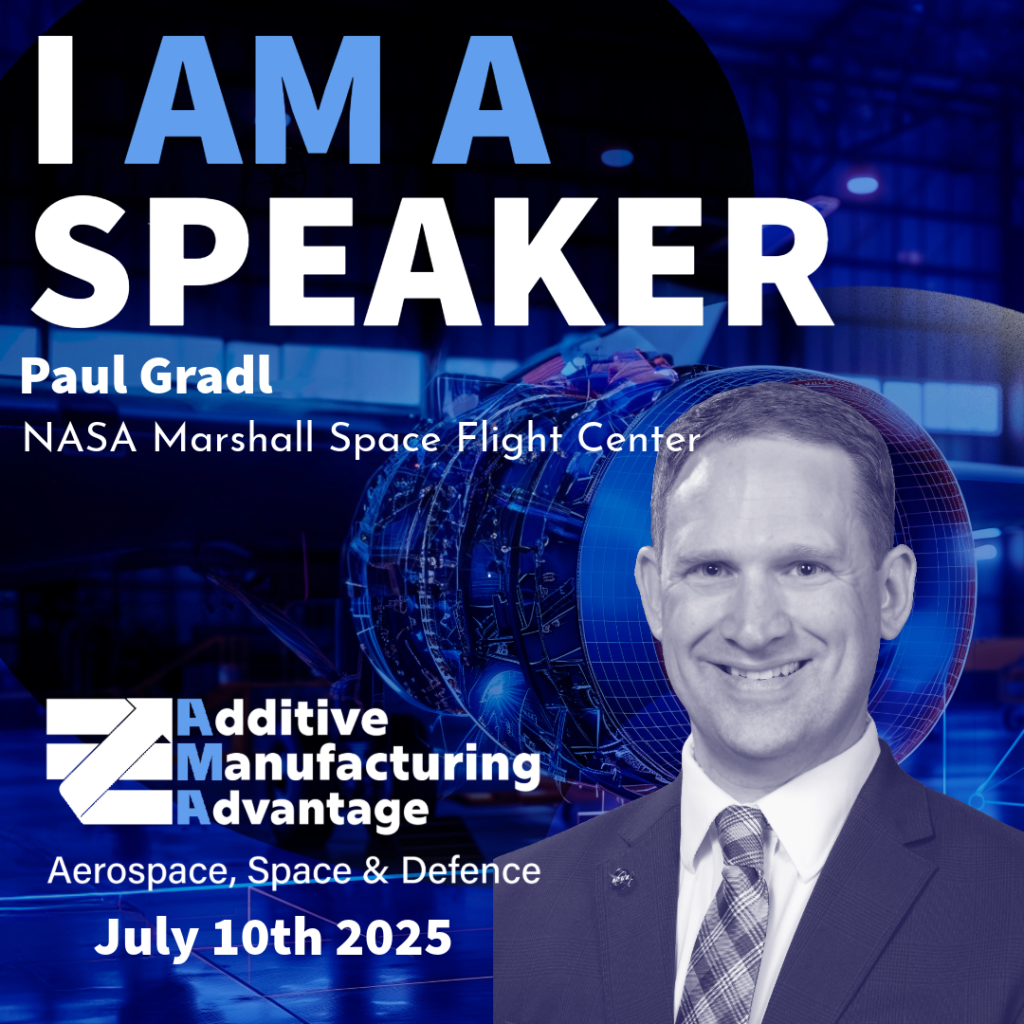
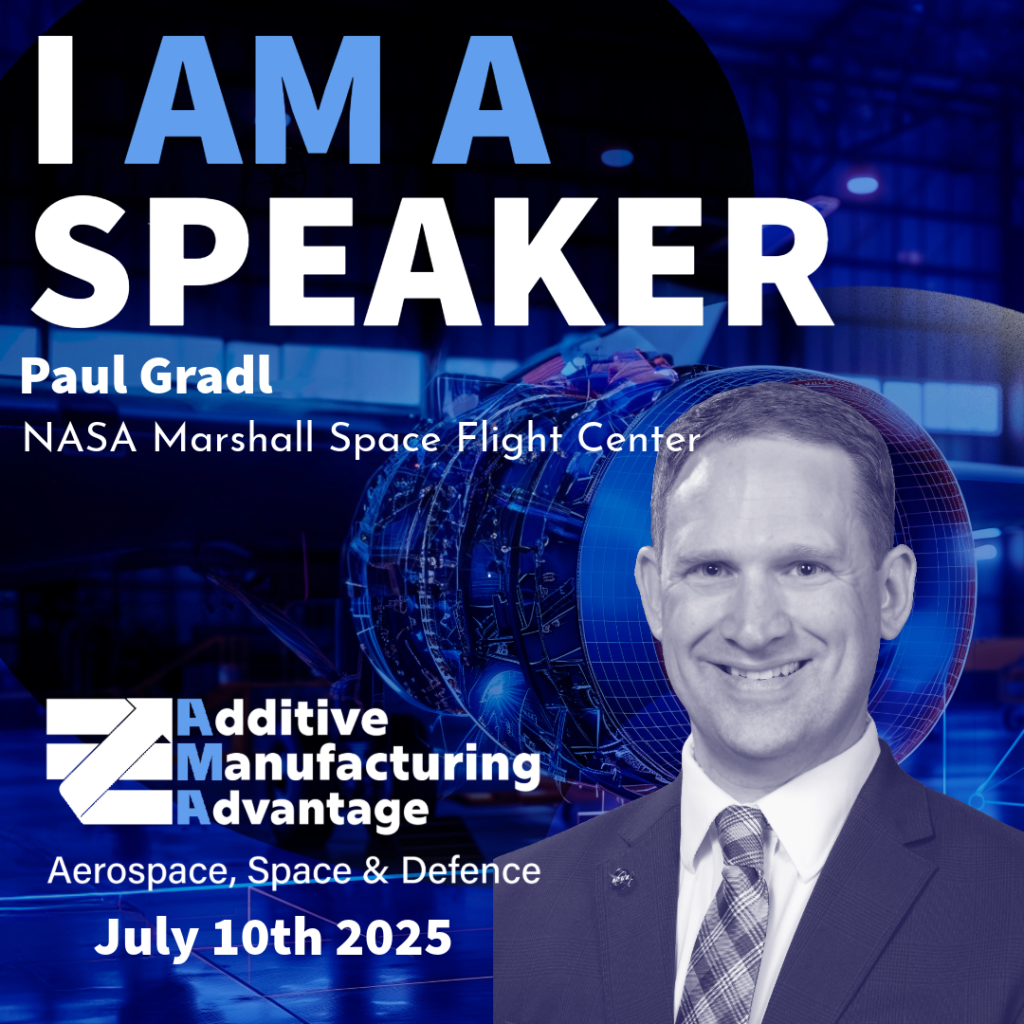
NASA pushes additive manufacturing frontiers with multi-material propulsion systems
NASA’s additive innovation is not limited to material discovery. Its invention of the year was a multi-material, multi-process thrust chamber liner assembly, produced using a combination of powder bed fusion, laser-directed energy deposition (DED), cold spray, and composite filament winding. This hybrid structure includes both axial and radial transitions between materials, allowing for locally tuned thermal and mechanical properties.
“We were able to combine three different materials and several different processes,” Gradl said. For example, high thermal conductivity copper alloys are used on interior surfaces, while superalloys with high strength-to-weight ratios are applied externally. A polymer matrix composite overwrap, typically carbon fibre, delivers a 40 percent weight reduction and structural reinforcement.
Gradl emphasised that AM is not displacing traditional processes indiscriminately. “We’re only replacing [them] where it makes sense, where it has an economic advantage, or higher performance,” he said. Increasingly, additive serves as a complementary technology that enables designs and integration steps previously not feasible.
Yet multi-material builds present unique challenges. Engineers must manage differences in thermal expansion, residual stress, and phase compatibility. “You can create conditions where I might embrittle the material, or have low ductility and actually crack the material,” Gradl warned. “There’s a lot of fundamental material science that we need to make sure we have the correct folks involved, it’s not just a crazy dream of a couple of engineers (although it might start like that).”
NASA’s experience points to a clear message: the path to high-performance, flight-ready components is paved with deep material science, multi-process integration, deep process understanding and control, and rigorous qualification, not shortcuts.
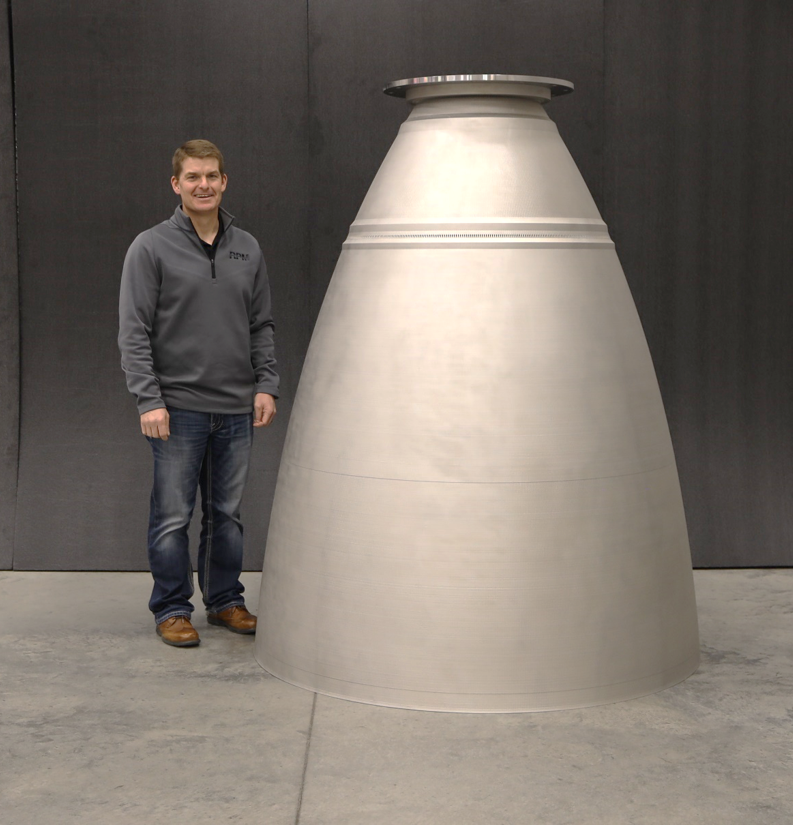
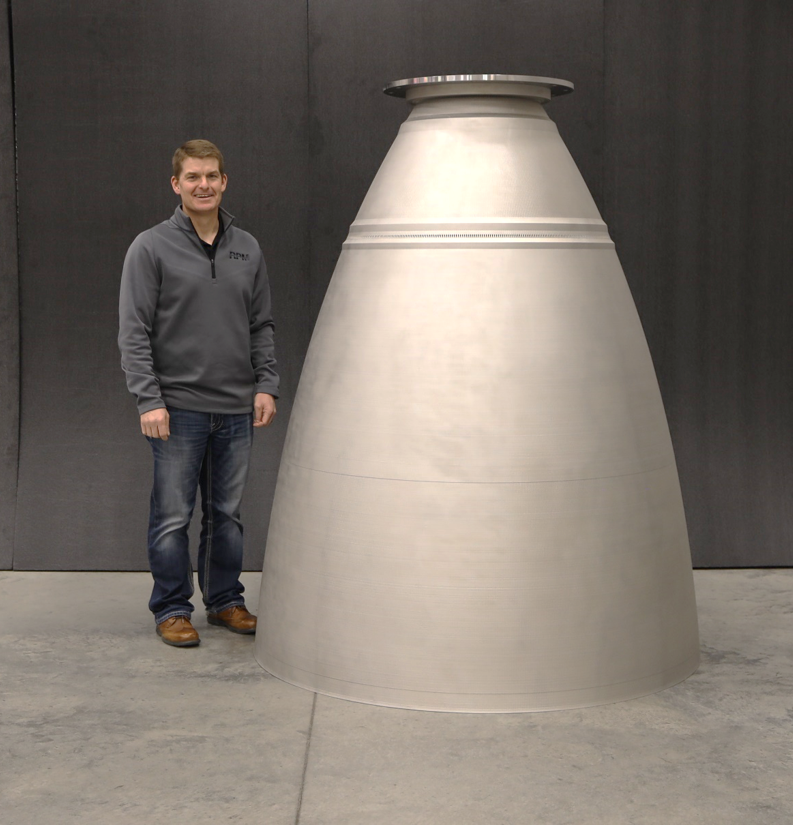
Insights into NASA’s advanced approach to additive manufacturing with post-processing, data sharing, and software breakthroughs
“You will not be successful in metal additive manufacturing unless you truly understand post-processing,” said Gradl. This includes not only machining and heat treatment but also inspection, powder removal, and defect mitigation across build stages.
In the case of large-format DED, many traditional inspection methods are no longer feasible. “CT scanning has come a long way for additive, but certainly at large scale, we don’t have access to scanners of that size,” Gradl said. Instead, NASA is exploring a mix of in-process melt pool monitoring, ultrasonic testing, and adapted X-ray techniques. The agency is also evaluating powder cleaning processes, such as vacuum cycle nucleation, to mitigate risks associated with residual powder and foreign object debris.
Design for additive manufacturing (DfAM) is undergoing a corresponding shift. Beyond overhangs and build orientation, engineers now integrate post-processing constraints into early-stage designs. For example, complex parts must be inspectable, machinable, and supportable in fixturing. “DfAM is much more than just the build side,” Gradl said. “We need to design for inspection, powder removal, and machining.”
Topology optimisation and generative design tools are also being employed more widely, but with caution. “You need to have a good handle on your environmental loads,” Gradl noted, particularly in aerospace applications where both input loads and material properties carry significant uncertainty. Without that rigour, designs risk overcomplexity and fatigue issues that outweigh marginal performance gains.
“One of the things holding us back from more complex designs is the lack of validated fatigue, creep, and size-dependent material properties,” Gradl said. Despite widespread recognition of differences in build orientation, size effects in thin-walled or small-scale features are less well understood.
NASA’s influence extends beyond its own launch systems. Through Space Act Agreements, the agency is advising startups and established firms alike on process education and qualification frameworks. This includes teaching designers to account for feedstock variation, gas flow dynamics, and machine-specific quirks that can affect material performance. “Even where I position my parts on the build plate could ultimately affect my material property,” said Gradl.
To accelerate tech transfer, Gradl emphasised the need for more open collaboration around data. “It would be nice if industry and government could start sharing material properties and develop more publicly accessible databases,” he said. Proprietary secrecy around allowables, he warned, may be inhibiting broader industry growth.
Across both propulsion and satellite systems, additive manufacturing is now considered a strategic enabler. “I can really optimize for weight, and I have to be able to control these satellite systems,” Gradl explained, referencing the growing role of extreme temperature materials and GRX-810 for in-space propulsion.
The next wave of capability may come not from hardware but software and control. NASA is exploring laser beam shaping, green and blue wavelength lasers for specific alloys, and fine control over energy input to achieve tailored material properties and geometries. “How do I really control the laser to make unique geometries that I couldn’t make with standard parameters?” Gradl asked. “These will help introduce more complexity and potentially even unique material properties.”
“We’re past the hype,” said Gradl. “Companies are trying to make it real, and they’re running into cultural psychology roadblocks.” The problem is not necessarily a lack of capability but how organisations evaluate risk, define qualification, and decide whether to adopt new material systems or part designs. Even when additive offers a clear performance gain, institutional reluctance to depart from established materials or certification paths can slow progress.
As NASA continues to support additive implementation across industry, Gradl sees the role of communication and expectation-setting as critical. “We’re in a unique spot,” he said. “We can openly talk about what’s working and what’s coming, and help companies think about how they might want to use multi-material additive manufacturing or new processes.” Public-private partnerships will be key to translating laboratory-scale innovation into operational advantage.
Join AM defense experts on July 10th at Additive Manufacturing Advantage: Aerospace, Space & Defense. Spaces are limited for this free online event. Register now.
How is the future of 3D printing shaping up?
To stay up to date with the latest 3D printing news, don’t forget to subscribe to the 3D Printing Industry newsletter or follow us on Twitter, or like our page on Facebook.
While you’re here, why not subscribe to our Youtube channel? Featuring discussion, debriefs, video shorts, and webinar replays.
Full Scale RS25 Additive Nozzle Liner printed by DM3D Technologies. Photo via NASA.