The Centre for Industrial Photonics (CIP) at the University of Cambridge’s Institute for Manufacturing (IfM) has developed an AM technique known as Laser-Assisted Cold Spray (LACS). This method enables high-precision deposition of coatings and the repair of components, with potential applications across industries such as aerospace, energy, biomedical, and process manufacturing.
By reducing material waste and energy consumption, LACS also offers a sustainable alternative to conventional manufacturing processes and may support efforts to lower industrial emissions.
“The potential applications for LACS are limitless and we are motivated to deliver a technology that can significantly aid in the transition to net zero, through both a more efficient, low-waste manufacturing technology and the doors it opens for sustainable product development,” said Professor Bill O’Neill, Project leader.
Additive Manufacturing is reshaping the future of the energy sector, including nuclear, renewables, oil and gas, turbomachinery, and beyond. Additive Manufacturing Advantage: Energy is a one-day, online event bringing together industry and experts. The call for speakers is now open.
Limitations in Conventional Cold Spray and the Evolution Toward LACS
Initially, the CIP team was working with conventional cold spray techniques, using nitrogen as the carrier gas to deposit powder materials. However, when attempting to coat or repair high-strength components made from materials such as titanium and aluminium alloys, they found that helium was essential for achieving optimal deposition. Despite its advantages, helium posed significant challenges—its cost (around £80 per minute of operation) and the limitations of recycling equipment, which restricted the maximum size of parts that could be processed.
“Imagine trying to apply a coating to a section of airplane cladding. Being able to do that within the constraints of a helium-recycling system is just unrealistic. We needed to find a more practical solution for these high-strength materials, and that’s when we started investigating using lasers,” said Dr Andrew Cockburn, Senior Research Associate at CIP.
The challenge led the team to develop LACS—an AM technique that uses localized laser heating of a supersonic powder stream to deposit metals and cermets for building, coating, or repairing parts. By lowering the substrate’s yield stress, the laser enables solid-state bonding without melting, resulting in stronger, more reliable coatings.
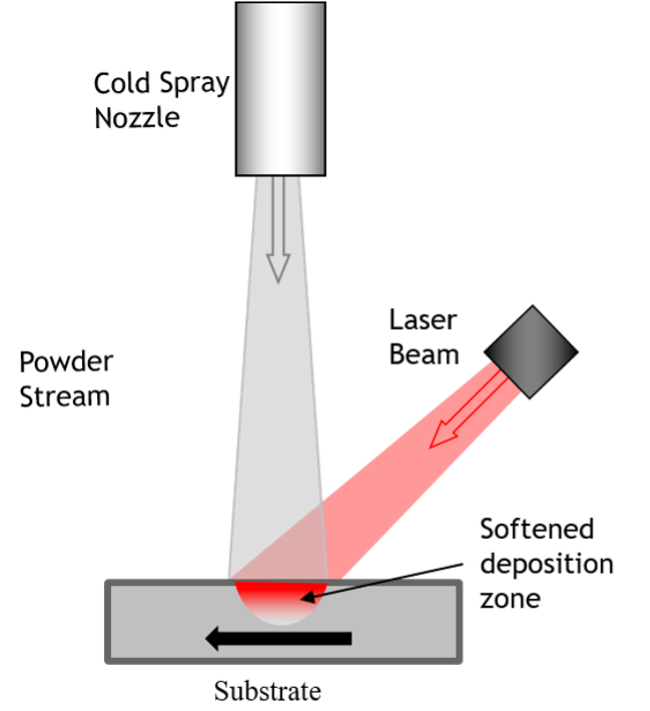
Image via University of Cambridge.
Advantages of LACS Over Traditional Cold Spray
In addition to improving deposition efficiency and bonding strength, LACS deposition occurs at a lower particle velocity. This helps preserve the powder’s original structure in the coating, benefiting sensitive materials such as nano-structured coatings and rare earth magnets.
LACS also expands material compatibility by enabling the deposition of harder and more challenging materials, including cermets, refractory metals, and oxidation-resistant alloys, which typically have poor adhesion in standard cold spray.
The laser’s thermal input reduces residual stresses within the coating, enhancing mechanical properties and minimizing porosity, thereby improving the structural integrity and durability of the deposited layer. The process is efficient, allowing coatings to be applied at rates up to 10 kilograms per hour, and it operates at lower overall gas temperatures—between 400 and 700°C compared to up to 1200°C for conventional cold spray—reducing power consumption and simplifying system design.
Finally, through the use of customized powders and graded compositions, LACS enables fine-tuning of coating properties to introduce specialized characteristics such as magnetism, solid-state lubrication, and enhanced wear resistance, while also reducing stresses at interfaces between dissimilar materials.
LACS Applications in Aerospace Manufacturing and Repair
LACS’s ability to both manufacture and repair custom parts makes it particularly well-suited for the aerospace industry. Traditional manufacturing often requires producing all parts for a model in a single batch and storing them, which creates two major challenges: high warehousing costs and limited spare part availability once inventory runs out. LACS offers a cost-effective, sustainable alternative by enabling in-situ repairs or full remanufacturing of components from existing bases.
Conventional repair methods such as welding are often unsuitable for high-performance materials like 6000-series aluminium, as the heat involved can weaken the repaired area and reduce its structural integrity. Bill O’Neill and his team have shown that LACS’s low-temperature, localized laser heating enables new material to be added without compromising the original part. Moreover, LACS systems can be programmed to build parts directly from digital models, allowing for rapid production of complex geometries.
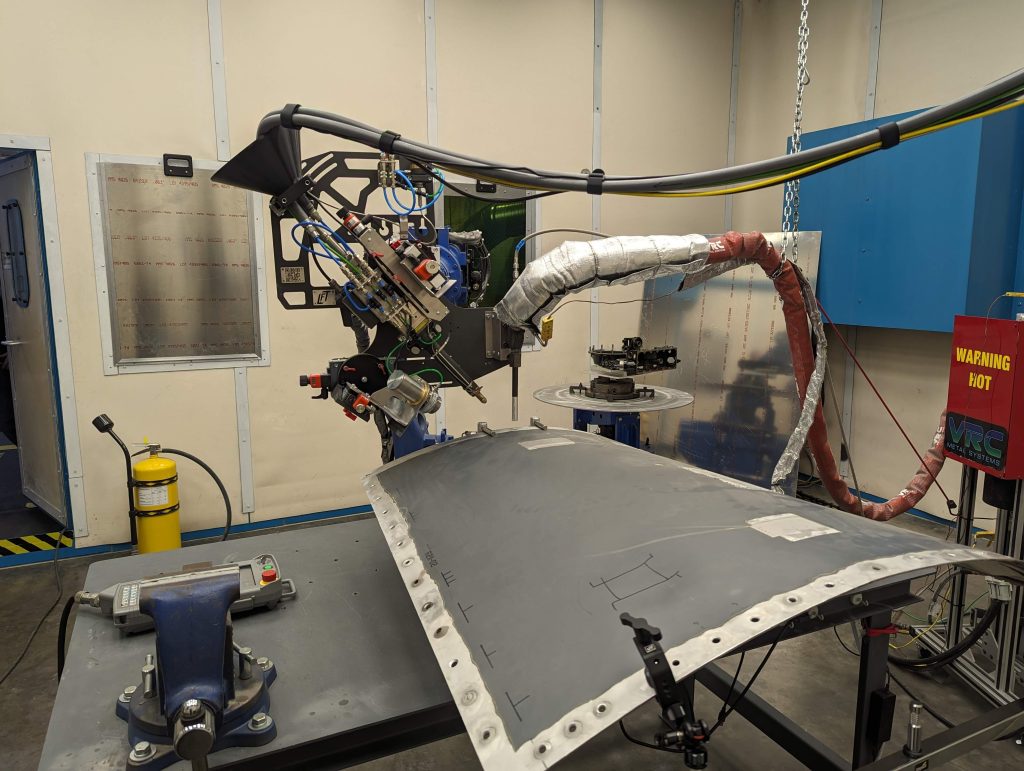
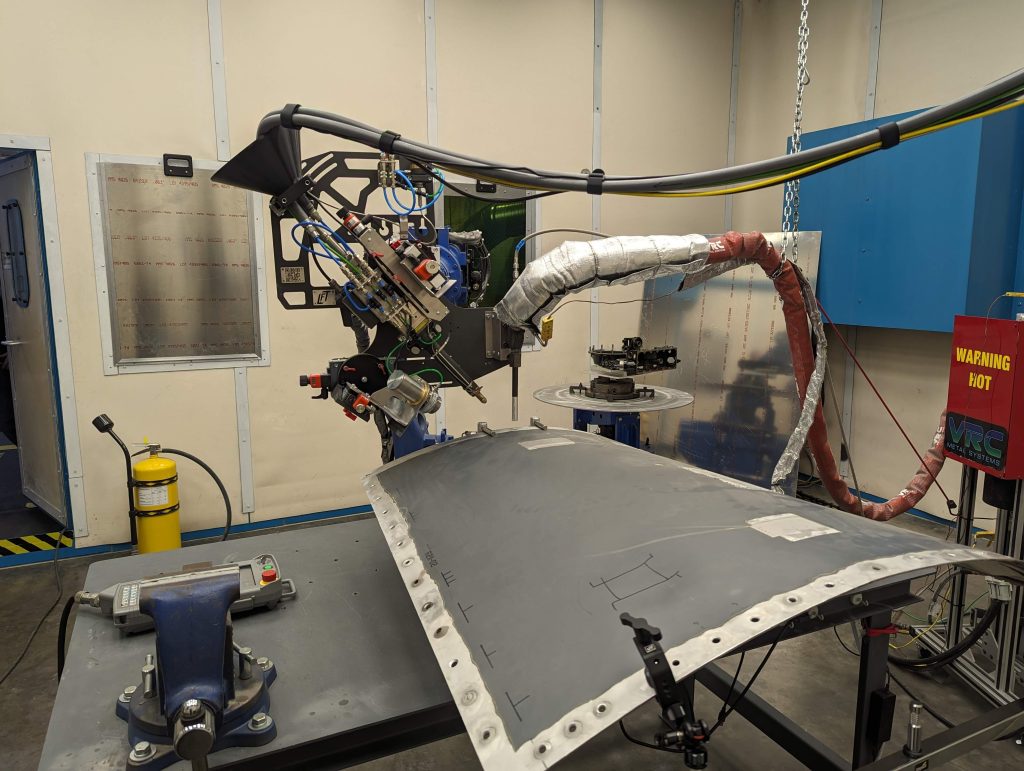
Expanding the Horizons of LACS
The CIP team’s next objective is to advance LACS technology to enable the 3D printing of complex shapes. To achieve this, they are exploring options such as mounting the workpiece on a robotic arm for full 3D movement and improving control over the powder stream’s direction to produce precise, smooth edges.
“Currently, we have little control over the shape of deposition of the powder. This is not an issue for coatings but presents a significant restraint for part-building applications. Our next goal is to find a solution to this limitation, and we already have some very promising results,” said Bill.
3D Printing Sprays
As research institutions like the University of Cambridge advance laser-assisted variations of cold spray for precision and repair, commercial manufacturers are also scaling cold spray for industrial and field-based applications.
In 2024, Australian metal 3D printer manufacturer SPEE3D introduced the TitanSPEE3D, its latest cold spray-based additive manufacturing system. Designed for large-scale production, the printer offers significant build volume and design flexibility. It can fabricate sizable metal components that would traditionally require casting, reducing production timelines from months to just days. Paul Maloney, Chief Revenue Officer at SPEE3D, described the TitanSPEE3D as a “game changer” for industries dependent on casting, stating it enables 3D printing “quickly, sustainably, and at a competitive cost.”
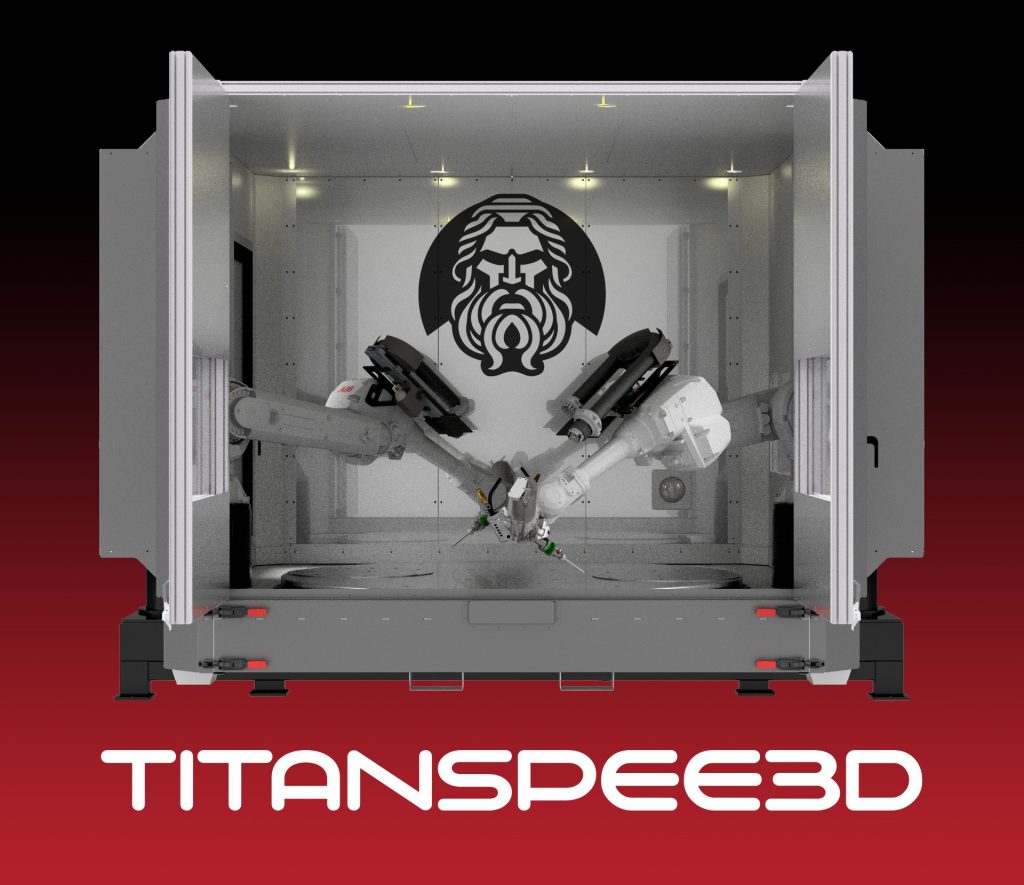
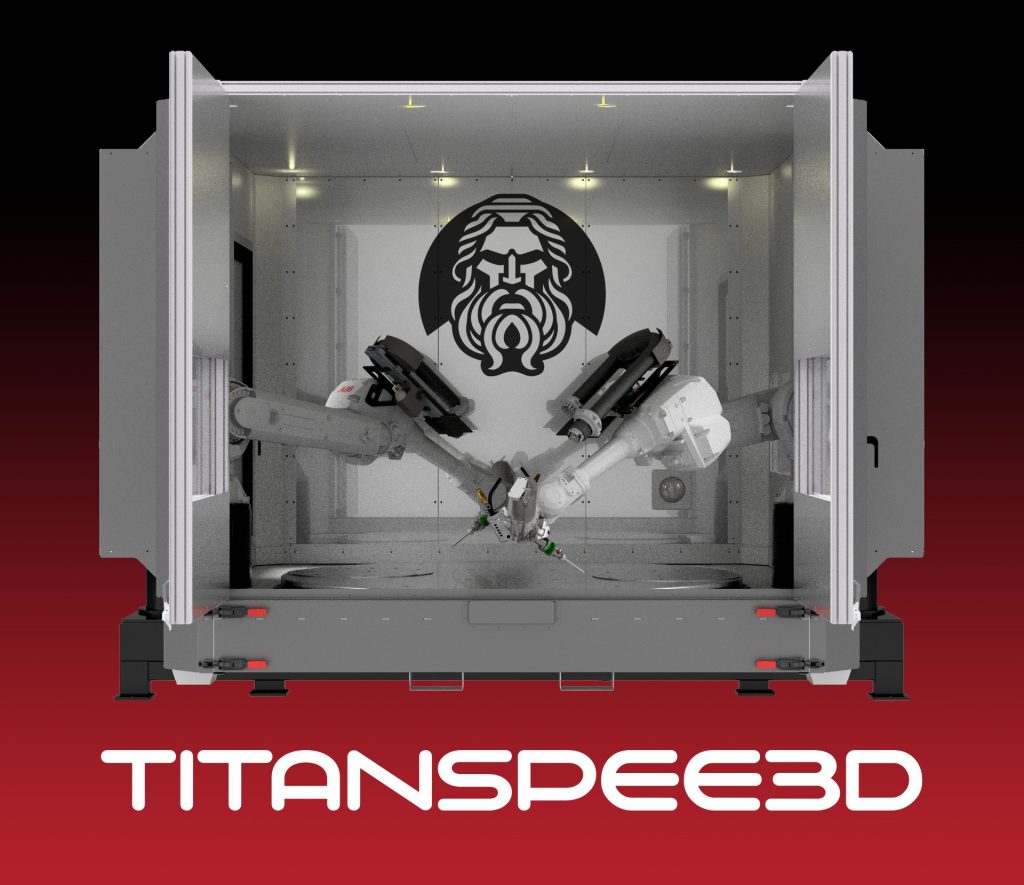
In a separate demonstration of its cold spray capabilities, SPEE3D successfully operated its containerized XSPEE3D system in sub-zero conditions during the U.S. Department of Defense’s Point of Need Manufacturing Challenge in Melbourne, Australia. Tailored for use in remote and extreme environments, the XSPEE3D employs Cold Spray Additive Manufacturing technology, propelling metal particles at supersonic speeds to produce high-density parts—without the need for lasers or inert gases. Encased in a standard 20-foot shipping container and requiring only a power supply, the system enables rapid, on-site production and has been validated as a practical solution for field-based manufacturing, including battle damage repair and large-component fabrication under harsh conditions.
Join our Additive Manufacturing Advantage (AMAA) event on July 10th, where AM leaders from Aerospace, Space, and Defense come together to share mission-critical insights. Online and free to attend. Secure your spot now.
Who won the 2024 3D Printing Industry Awards?
Subscribe to the 3D Printing Industry newsletter to keep up with the latest 3D printing news.
You can also follow us on LinkedIn, and subscribe to the 3D Printing Industry Youtube channel to access more exclusive content.
Featured image shows LACS equipment set-up to add a coating to repair a panel aircraft wing. Photo via University of Cambridge.