The costs of making things in space — and getting them back to earth — is high. But infrastructure to bring down the costs is being built.
“You wouldn’t think anything about maybe manufacturing in China or India, but actually the International Space Station is closer – it’s 250 miles in the sky. So this is really not as crazy as you would imagine,” says Nicole Wagner, CEO of LambdaVision, a Connecticut-based startup using microgravity to create multi-layered membranes that replace crucial parts in the retina, restoring sight to people suffering from vision loss.
The limits to manufacturing on Earth are usually thought of as money, process or technology. But in many sectors, gravity is a significant hindrance, akin to tying one hand behind our backs. Matter behaves differently when constantly being pulled in one direction. In areas like optics, pharmaceuticals and semiconductors, taking gravity out of the equation can result in much higher quality — and higher value — product.
A number of startups are already testing how a space manufacturing market might work.
Microgravity, macro impact
The obvious starting point is low-volume, high value products where zero-gravity manufacture makes the most difference.
Microgravity would allow for new pharmaceuticals to be made with superior crystal structures, given that protein crystallisation can be made with higher purity. Cell cultures may grow differently in microgravity, or their genes might express differently because of radiation in space, allowing scientists to gain insights. Organoids – or 3D models of organs at miniature scale – require complex manufacturing processes on earth which may not be necessary in space.
Optical fibres and thin films can be made more uniformly, reducing gravity-derived defects in semiconductors. Less gravity means that material being made will have less concentration along an ideally uniform plane, something that would benefit a wide range of applications.
Even for something like skin care, microgravity may help in the development of active ingredients in cosmetic products like vitamins or retinol, while yeast for extracts may grow faster and have higher metabolic production in microgravity.
New ways could be discovered to produce novel, more effective probiotics, which may express themselves differently in space.
Astronomical cost?
Getting things safely into space and back again, however, is a hurdle, and high costs make space manufacture challenging to scale.
Beyond the costs of the actual launch, there are three major drivers of cost when doing science in space, according to Wagner. The first is astronaut time – maybe the most constrained resource. Every hour of an astronaut’s time is expensive and has an opportunity cost in terms of everything else they need to do. Another driver is mass, as payloads are still costed per kilogramme launched and even with the cheapest flight providers like SpaceX, who leverage reusable rockets to drive down costs, each kilogramme is expensive. Lastly, similar to astronaut time, energy is also a constrained resource on the International Space Station and also carries an opportunity cost.
LambdaVision has sought to minimise that cost by creating an autonomous system that doesn’t require any astronaut time. The payload is small, with the minilab roughly the size of a shoebox, and energy efficient. Other, more involved technologies and experiments that may require human intervention would incur higher costs.
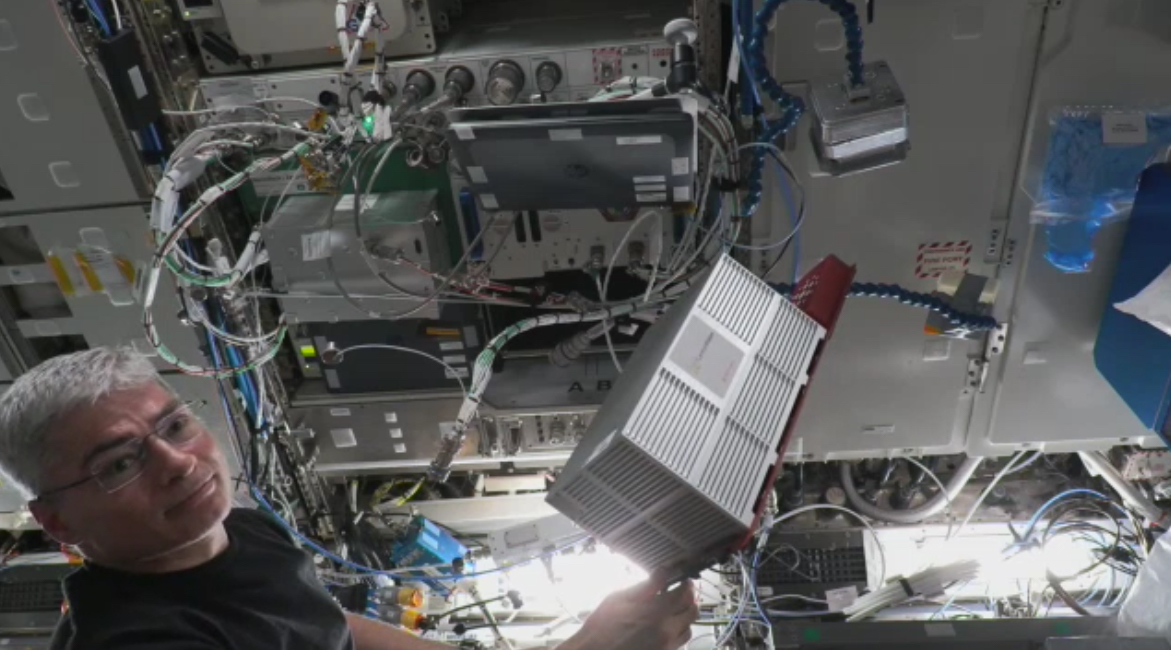
Another consideration is that the reliance on the ISS as a lab means that companies are also held hostage to its schedule. There are far more opportunities to send something up to the ISS than there are to bring things back down and, as the world recently saw when astronauts were marooned up there for months, there can be sudden, significant changes to plans.
Outside help
There is a growing market for in-space facilitators and partners that help companies actually implement their experimentation activity. Companies like Space Tango and Redwire Space create the in-space platforms to carry out the work and take charge of liaising with the various players, the launch companies, the customers and the space station stakeholders in order to make things happen, removing that burden from startups themselves.
In LambdaVision’s case, Space Tango was the one who liaised trips across multiple carriers, including Northrupp Grumman and SpaceX.
Premium prices
Even when the unit economics are minimised and the volume can be maximised, items manufactured in space will be costly for end users.
But something that can restore one of your five senses, for example, will be highly price-inelastic if you’ve got the money to pay for it. This is especially the case when alternative treatments can be just as expensive, if not more, and ongoing. LambdaVision’s procedure is, if all goes well, a one-and-done affair.
While still in pre-clinical phase, having not implanted their hole-punch-sized retinal patch into patients yet, the manufacturing process is looking promising, and the layer-by-layer assembly could be applied to many other products.
Materials related to photovoltaic energy generation, toxin detection, biosensors and artificial organ generation could all benefit from a similar process.
Investors questions
LambdaVision has so far raised around $14m overall, through grant contracts and investor funding, and was part of the Seraphim Space Accelerator. Other startups like the UK’s Space Forge, which manufacturers high-performance semiconductor materials in space, recently raised $30m in a series A backed by investors like the NATO Innovation Fund.
“ We have a lot of tech-based investors that are also very enthusiastic about the research that’s going on in space, and for them I think a lot of the questions are around scale, the unit economics, the cadence of flights to the ISS or future LEO destinations, as well as understanding what this is going to look like from a regulatory perspective moving forward,” says Wagner.
Another thing they tend to ask is the extent to which microgravity conditions can be replicated on Earth, without the need to launch into orbit. The answer is not much. You can achieve small bursts that can range from seconds – on things like drop towers that suspend their contents for a moment – to slightly longer on parabolic flights, to up to several minutes on Blue Origin’s suborbital flights.
Any way you cut it, nothing on Earth can sustain microgravity long enough to be effective.
Can’t do it alone
For space manufacturing to scale however, there needs to be much more, and more specialised infrastructure that allows manufacturers to get material into space — and even more crucially — back down to earth again.
It is much easier to send things up to ISS (upmass) than it is to send them back down to Earth (downmass). There are more vehicles capable of launch than there are of re-entry, meaning the rate at which startups are currently able to get their products back is much less frequent, and recovery logistics are more complicated than launch logistics. Depending on what your technology is, it can also be pushed back in the queue.
Once a critical mass of infrastructure is in place, says Wagner, space manufacturing could scale up quickly. There could be more “shoeboxes”, or they could grow to microwave or refrigerator-sized units, massively increasing output.
Some startups, like Varda Industries, which is based in California and just this week raised a $187m series C round, is looking to vertically integrate the process by creating their own platforms to create pharmaceuticals in space.